 |
MAYO-JUNIO DE 2010 |
 |
|
|
|
 |
 |
|
- +Vitrificación para inmovilizar residuos peligrosos
-
- +Un lifting para tus mitocondrias
-
|
|
|
 |
|
|
|
|
|
|
|
|
|
 |
SERGIO BELLESTEROS ELIZONDO, JOSÉ R. PARGA BALLESTEROS
Y JESÚS MA. RINCÓN LÓPEZ |
Proceso de vitrificación |
Después de procesar térmicamente los residuos mezclados con sílice, óxido de sodio y óxido de calcio –de manera continua, y en un reactor de vitrificación– se funde todo a una temperatura entre 1300 y 1500 °C, y el resultado final es un producto vítreo y moldeable de color oscuro, parecido a la obsidiana, que es un vidrio natural. El proceso de vitrificación aquí propuesto se inicia con la recolección de residuos industriales peligrosos, continúa con su transporte legal, la consecuente recepción en la planta piloto, el proceso de tratamiento de vitrificación y, finalmente, la obtención de productos inertes con potencial para ser comercializados como materiales de construcción.
Los componentes resultantes son totalmente inertes y el producto final es estable a lo largo del tiempo; un ejemplo de ello es que no se empezó a pensar en esta tecnología hasta después de investigar y comprobar una decuado funcionamiento para eliminar la toxicidad de residuos peligrosos (figura 2).
El vidrio puede estar formado por cualquier elemento de la tabla periódica, en vez de llevar los componentes básicos que son sílice y sosa; en el caso de la vitrificación de los RP, la materia prima necesaria procede de las cenizas de los residuos; no obstante, es claro que ese producto no podrá ser utilizado, en ningún caso, para elaborar envases de alimentos, pero sí en losetas o agregados sintéticos de vitrocerámicos, aplicables en la industria de la construcción.
En varios países, la vitrificación es una tecnología implantada hace tiempo e, incluso, superada; por ejemplo, en Japón existen incineradoras de residuos sólidos municipales que cuentan con una planta de vitrificación anexa a la incineradora. En los Estados Unidos han ido más lejos, pues hacen la vitrificación in situ, introduciendo electrodos de grafito en los residuos, lo que permite la vitrificación, cuyo fundido se produce por conducción eléctrica.
En Querétaro, México, el Centro de Tecnología Avanzada (CIATEQ, A. C.) hemos desarrollado una tecnología de vitrificación de residuos peligrosos, mediante la inmovilización de las especies tóxicas presentes en los desechos, con lo cual se ha obtenido valores residuales por debajo de los límites permisibles que dicta la regulación mundial europea y la estadounidense. El resultado del proceso es un vidrio aprovechable en forma de productos comerciales (figura 3).
En el ámbito mundial, la mayoría de los hornos de vitrificación en uso son eléctricos o de plasmas de alta temperatura; en el primer caso, el arco producido por unos electrodos da lugar a un calentamiento hasta lograr la fusión de la mezcla; en el segundo, se provoca una ionización de gas que permite a la vez una temperatura más elevada hasta 15,000 °C. Estos sistemas de hornos consumen grandes cantidades de energía y su infraestructura es muy costosa.
En México, las ventajas del uso de carbón de coque nacional en la vitrificación de residuos peligrosos, propuesto por el área de equipos de procesos del CIATEQ (Unidad Bernardo Quintana, del Municipio del Marqués, Querétaro), radica en el ahorro del costo de energía, en comparación con los precios de los otros dos reactores de vitrificación. Si se utilizara un horno de arco eléctrico o de plasma para fundir una tonelada de sílice, se necesitarían 560 kilovatios hora (kwh), lo que representaría una gasto de 288 pesos; mientras que con el horno desarrollado por el CIATEQ, sólo se necesitarían 100 kilogramos de carbón coque, y la fusión del material tendría un costo de 507 pesos.
En comparación con los servicios de almacenamiento de residuos peligrosos, las empresas dedicadas a esta tarea cobran entre 1.5 y 2 pesos por kilogramo de material confinado; mientras que, con la tecnología del CIATEQ, sólo cuesta 60 centavos vitrificar cada kilo de residuos; otra ventaja es la independencia operativa respecto tanto de la disponibilidad de energía eléctrica como de la variabilidad horaria de las tarifas de la Comisión Federal de Electricidad, puesto que en horas pico de alto consumo el costo se eleva, por lo cual el horno del CIATEQ no está condicionado por las altas y las bajas en el consumo eléctrico.
Otro aspecto relevante es que, además del ahorro que para las empresas significaría la vitrificación de residuos, en vez de su almacenamiento, el proceso tiene un impacto positivo en el medio ambiente, pues al reducirse la cantidad de desechos por almacenar, no sería necesario seguir sacrificando extensiones del territorio nacional para
guardar los residuos de manera permanente. Con este proceso se evitarían los costos de almacenamiento en rellenos sanitarios y/o confinamientos, ya que el producto vitrificado final tendría aplicaciones en la industria de la construcción. En síntesis: si consideramos el ahorro del pago de depósito en confinamiento y el correspondiente a la vitrificación, y consideramos el aprovechamiento de los productos finales, se puede estimar que la vitrificación implicaría un ahorro de 40%, comparado con el costo del proceso de almacenamiento de residuos.
Por ser de naturaleza térmica, el proceso de vitrificación implica una emisión de gases contaminantes que es controlada a través de un sistema de vía seca; es decir, mediante un mecanismo que no utiliza agua para el lavado de las emisiones, el cual consiste en hacer pasar la corriente de emisiones de gas (SOX –óxidos de azufre–, NOX –óxidos de nitrógeno–) en una columna de cal viva, con el fin de enfriar y neutralizar dichas emisiones, lo que puede ser complementado con la instalación de filtros catalíticos para tratar otras emisiones más complejas como compuestos orgánicos volátiles, dioxinas y furanos, por ejemplo.
Las experimentaciones llevadas a cabo en el CIATEQ han dado un rendimiento de 7 ton/hora, de residuo tratado en continuo –24 horas durante 15 días y sólo un día para el mantenimiento del equipo–. Dichos resultados han atraído el interés de las industrias metalmecánica y metalúrgica, pretendiendo difundir esta tecnología con el fin de despertar el interés de las autoridades gubernamentales y demás empresarios de parques industriales, procurando que se realice la instalación de plantas de vitrificación públicas y privadas que, sobre todo, beneficien el medioambiente.
|
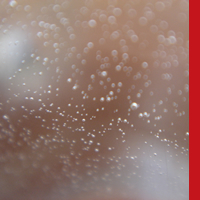 |
|
 |
|